How to find the right fittings for your hydraulic system
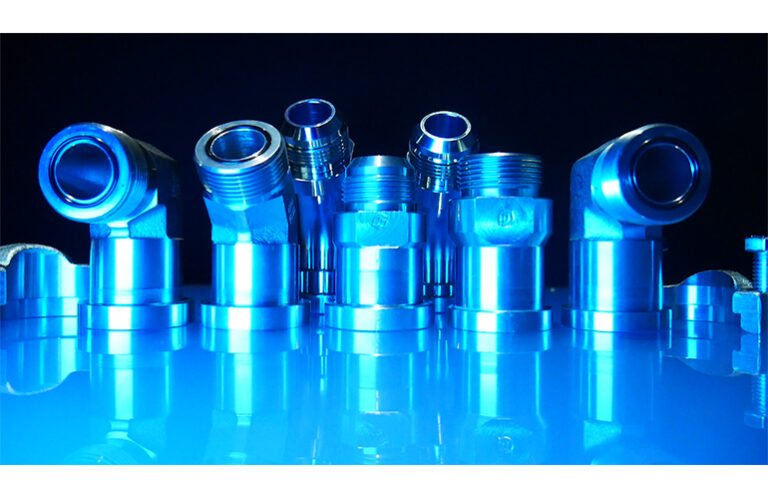
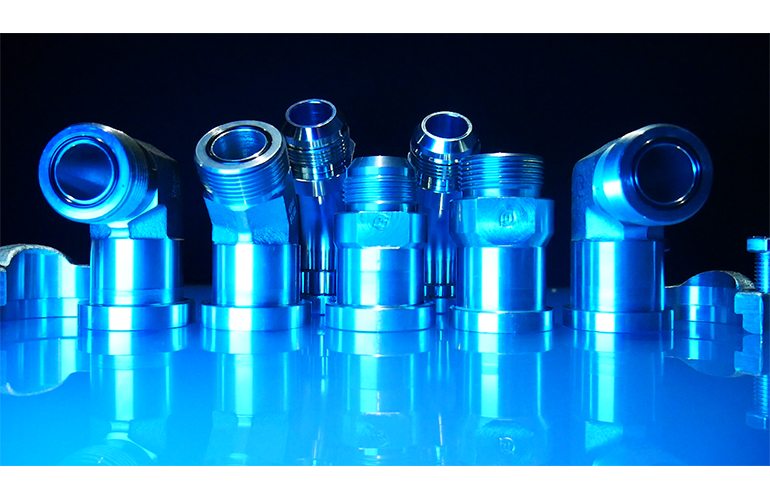
Making the shift to connections with elastomeric O-ring seals is the focus in today’s fluid power industry. But before following everyone’s lead, it’s important you understand the connections to properly use them within your application, especially since hydraulic systems use many types of fittings and adapters within different sealing methods and thread forms.
Why use a flange fitting
Hydraulic connections are used to prevent leaks and other possible failures within high-pressure applications, especially in larger sizes. Flanges are used when designing for easy connection between the hose, tube and pipe. It’s where flexibility is needed the most within the system.
Flange connections are typically used in applications featuring exceptionally high pressures when using pipe or tubing with an OD over 7/8 in. They may be bolted together to mate two sections of pipe (tube or hose), or bolted or screwed into the component to secure a flange fitting or section of pipe. Flanges can also be disassembled for easy access to modify the system, clean or inspect it. Certain flanges may also be permanently welded together or to the port section of the component like a motor housing or a valve port. More commonly, a flanged joint is made by bolting two flanges together with a gasket in-between to ensure a secure seal.
The reason for their use is to connect ports directly without having to use threaded connectors or adapters. They are good for hard-to-reach areas, quick maintenance and rigorous hydraulic applications. Flange fittings are also the best option for hose end connections that have bends and are subject to high lateral forces.
But before any hose, tube and pipe are assembled, it’s important to identify the ends of the ports and connectors. It helps to ensure the connection will be safe. The Society of Automotive Engineers (SAE)and International Organization for Standardization (ISO) help you to identify any specific problems when making these connections.
Flange fittings with O-rings produce minimal leakage when they are matched correctly. The elastomeric seal is located within the groove to close the fluid. These fittings include the SAE straight thread, face seal, ISO 6149, SAE J518 (Code 61 and Code 62) flanges, etc.
Common types of flange fittings and components:
SAE J518 flange fittings — SAE J518 is used throughout the world to connect larger diameter tubing and pipe within the fluid power industry. Minus the bolt sizes, SAE J518 flanges are interchangeable with ISO 6141, DIN 20066 and JIS B 8363. These flanges come in two pressure classes. The standard is ISO6162, and it includes SAE Code 61 and Code 62. This is important because if the wrong flange is installed, you could have serious problems in your system because a SAE Code 62 handles up to 6,000 psi and a SAE Code 61 handles up to 3,000 to 5,000 psi.
Captive flange clamps — Captive flange clamps are often used when connecting tubes, pipes or hoses. They slip over the flared tube and are easily connected to the mating flange or component. These types of clamps are commonly used with MJ-flange straight fittings because there is a smooth clearance to slide over the fitting and sit on the flange head.
Split flange clamps — Split flange clamps are made from two interlocking pieces, fitting securely together with nuts and bolts. Since they have two pieces, these types of clamps are used to reinforce weak areas within the tubing and pipe. They can add an attachment where traditional flanges could not. You can buy these flange fitting clamps in kits (either for Code 61 or Code 62). A kit could include the two pieces, O-ring face seal (ORFS) and four bolts and washers.
These common types of flange fittings and components are much less likely to loosen when there is proper load distribution of clamping around the flange head.
ORFS fittings are reliable
Fittings and component assemblies are required to work in harsh environments, such as corrosive offshore applications to extreme temperature and pressure fluctuations. ORFS fittings are reliable because they include elastomeric seal O-rings. It’s one of the best choices for a leak-free connection.
As the name implies, ORFS, or (O-ring Face Seal) fittings incorporate an O-ring at the face of the fitting. Made to SAE J1453 standard, ORFS connections are commonly manufactured in carbon, nickel plated carbon and stainless steel and typically use elasteromeric seals, such as Buna-N or Viton, 90 Durometer O-rings that seat into a groove in the face of the fitting.
When the o-ring compresses between the o-ring face of the fitting and flat face of the mating ORFS fitting or the formed tube, a leak-tight seal is created. When the connection is tightened, the O-ring compresses against a flat face of mating fitting or tube.
While custom-made stainless is available, standard ORFS fittings and flat face sleeves are made from plated steel or stainless steel. First designed for off-road construction, ORFS fittings are now used in other transportation applications. ORFS fittings are good for high pressures that are subject to flexing or pressure surges, such as construction, agricultural, oil and gas, mining and the high-performance industrial markets. They are also the preferred connection for high vibration systems because the O-ring is soft and absorbs shock better than metal-to-metal sealed fittings.
Causes of hydraulic system leakage
If you’re having hydraulic system leakage, know that it is rarely caused by the fitting itself. The primary contributors to system leaks include improper installation, poor system design, component quality and system abuse.
It’s important that you understand this because the result can be costly. Not only is it costly from an equipment and operation standpoint, but it’s also costly from a loss of fluid standpoint. If an operation is running 24 hours a day and hydraulic oil costs $25 a gallon, the cost of leaking fluid can be significant. System design is the first place to start when preventing a leak. The right components must be selected to reduce the incidences of leaks and connection failures. When preventing hydraulic system leakage, review the following areas:
Application — Your environment determines the fitting design and selection. For example, stainless steel or other protective coatings can extend the service life in corrosive environments. Even the choice of O-ring material must meet the system conditions. A fluorocarbon or other material may need to be specified over Buna-N in some applications
Pressure — The dynamic pressure rating of the flange fitting assembly must be equal to or higher than the system’s pressure. Fittings are rated at a 4:1 design ratio, which applies to normal operating conditions for withstanding moderate hydraulic and mechanical shock. For severe vibration and shock, a “de-rating factor” should be applied directly to the dynamic pressure of the fitting.
Temperature — The operating temperature for fittings and O-ring seals is dependent on the plating and the metal and seal materials.
Finding what’s right for your application
If you’re ordering quality flange fittings and ORFS components from a reputable manufacturer, then you should be in a better place than most. It’s important to collaborate with your supplier to make sure that you choose what is good for your application.
The right products are available for your system. Just make sure you are looking for best-in-class products from certified manufacturers who can respond quickly to your growing needs while still meeting and exceeding industry standards. The design and durability of each flange fitting and component will assure long-lasting service, even in corrosive and abusive environments.