What is the role of pressure test fitting in full hydraulic system equipment?
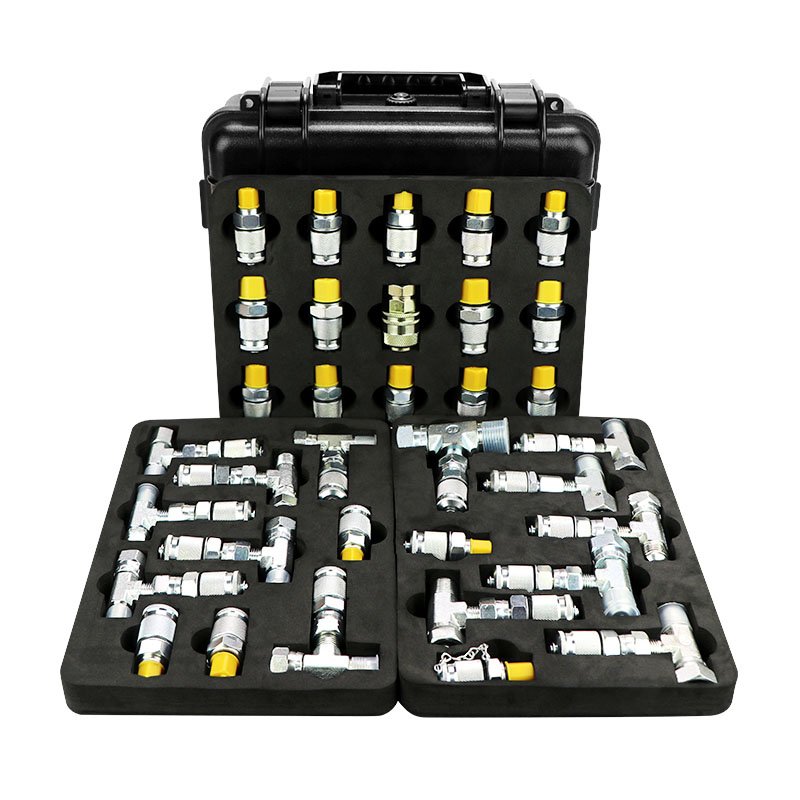
In order to simplify the mechanical structure design of modern machinery and equipment, its power transmission system often adopts full hydraulic drive: it makes the overall layout more reasonable, the structure design is simpler, the system operation is more convenient, the quality is more reliable, and the power is more powerful. , Debugging and maintenance is also more convenient, so it is favored by more and more users.
In order to fully understand the working conditions of the full hydraulic system, when designing the full hydraulic system, a pressure measuring point is often set in the oil circuit of the full hydraulic system, and a pressure testing pipe fittings is arranged at the pressure measuring point to measure the oil circuit. Whether the pressure value is within the normal range, so as to quickly measure the pressure and eliminate the fault.
How does the high pressure test fittings work
There is a self-sealing valve in the pressure test port fittings. When used alone, the self-sealing valve will automatically close due to the action of the spring; the self-sealing valve can be opened after being connected to a measuring hose or measuring connector with a thimble, which is used for high-pressure or low-pressure fluid systems. Sampling and system pressure detection. The working pressure can reach 63MPa, and the BP pressure can reach 250MPa.
What does it do?
hydraulic pressure test fittings are mainly used in pipeline systems in full hydraulic systems, and are used for pressure monitoring and detection, exhaust, sampling in high pressure and low pressure systems. Pressure measuring joints are mainly used in construction machinery, agricultural machinery, hydraulic systems, testing equipment, etc.
For example: hydraulic excavators have more complicated hydraulic systems and controls, so how to judge hydraulic failures?
As shown below:
At this time, it is necessary to set up a high pressure test fittings, measure the hydraulic pressure at the pressure measuring point, and find the source of the fault! The pressure test joint can withstand the pressure test in the hydraulic system, which is essential for the smooth and reliable operation of the hydraulic device. Therefore, the pressure test point fitting is widely used as the standard configuration of the current hydraulic system.
Is it necessary to set up a hydraulic pressure test fitting?
It adopts a fully hydraulically driven walking system. The entire hydraulic system is integrated by hydraulic motors, hydraulic actuators, hydraulic valves, oil pipes and other components. The system is very complex. The pipeline from the oil pump to the hydraulic actuators is long, and the hydraulic oil flowing distance is relatively long. long. There are changes in liquid flow direction and velocity, and pressure loss is unpredictable. System debugging is difficult and maintenance is inconvenient. Therefore, in the design process, the characteristics of the full hydraulic system should be fully considered, pressure measurement points should be set, and high pressure test fitting should be configured.
Why install pressure test fittings?
1. Facilitate fault diagnosis of full hydraulic system
The full hydraulic system is complex, the number of hydraulic motors and integrated valve blocks is large, and the probability of failure is high. Once a failure occurs, quickly identifying the cause of the failure is the key to troubleshooting. The installation of bsp test fitting in the full hydraulic system can be achieved by Pressure test at the pressure measuring point to determine the possible cause of the failure. Judging the range of possible failures of the full hydraulic system with the help of pressure test compression fitting will be very beneficial to find out the causes of the failures and eliminate the failures.
2. Improve the working performance of the full hydraulic system
There are many pumps and motors in the full hydraulic system equipment, and the hydraulic oil flow rate is large. Due to the limitation of the mechanical structure, the hydraulic oil flows in the oil tank for a short distance, and the bubble exudation rate is low, and a large number of bubbles will be brought into the pipeline again. A test point fitting is installed in the hydraulic pipeline, and the gas accumulated in the higher part of the hydraulic pipeline is released through the test point fitting. In order to make up for the defect of low leakage rate of air bubbles in the fuel tank, it is very beneficial to reduce hydraulic shock and improve the working performance of the system.
There are many hydraulic components and executive parts in the full hydraulic system equipment, and the system is more complicated. It is necessary to fully consider the mechanical structure, working environment, special requirements and various problems that may arise in the design of the full hydraulic system. It is very necessary to comprehensively apply various methods to improve the performance and maintainability of the system. Appropriate application of hydraulic system equipment to improve the quality and reliability of equipment, in general, the advantages outweigh the disadvantages, and it is beneficial to the debugging and performance improvement of the full hydraulic system.
Are you using pressure test fittings? Are there any skills or knowledge do you want to share?